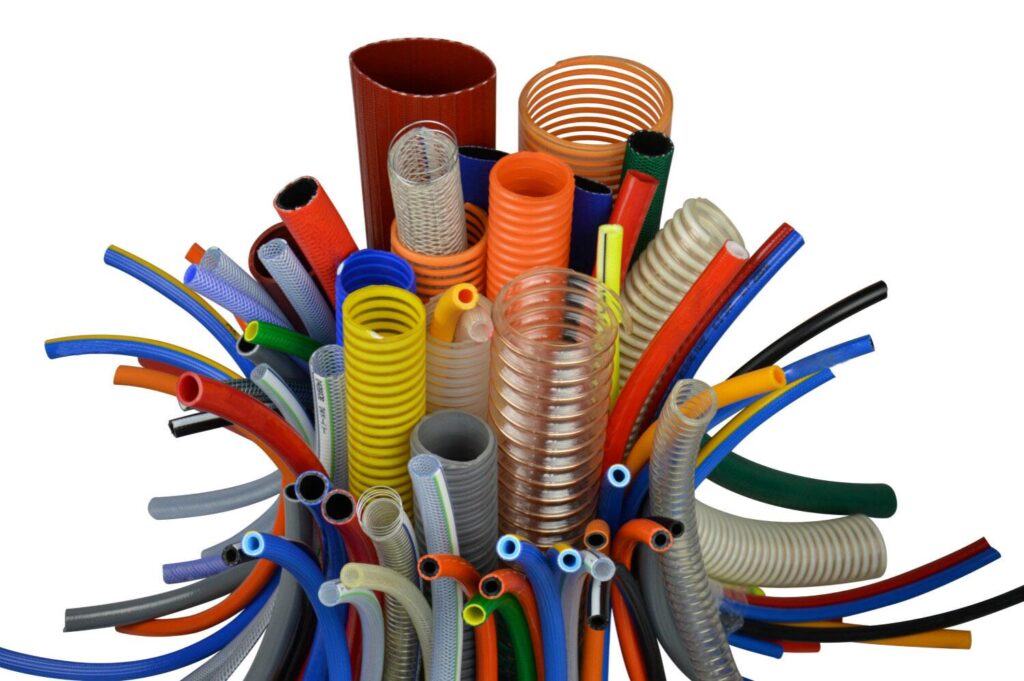
PVC hoses play a critical role in a wide range of industries, from agriculture to construction, automotive to chemical processing. Their flexibility, durability, and ability to withstand harsh conditions make them indispensable for transporting fluids, gases, and other materials. But what makes a PVC hose so reliable? It all starts with the transformation of raw materials into a robust, reinforced product. In this article, we’ll explore the journey of PVC hoses, from their humble beginnings as raw materials to their final form as industrial-strength solutions.
Step 1: The Raw Materials
Polyvinyl chloride (PVC), the core material used to make PVC HOSE Manufacturer , is a type of plastic created through a polymerization process. The main ingredients used to produce PVC include ethylene, derived from oil or natural gas, and chlorine, sourced from salt. When these two elements are combined, they form vinyl chloride monomer, which is then polymerized into polyvinyl chloride, or PVC.
However, PVC alone cannot meet the wide range of requirements for different hose applications. To make it more flexible, strong, and weather-resistant, manufacturers add plasticizers, stabilizers, and other additives to the raw PVC material. These additives play a crucial role in determining the specific properties of the hose, such as its flexibility, chemical resistance, and durability.
Step 2: The Extrusion Process
Once the PVC compound is prepared, it undergoes the extrusion process, which is the heart of PVC hose manufacturing. During extrusion, the PVC compound is heated and passed through an extruder, a machine that shapes the material into a continuous tube form. The extruder uses a specially designed die that gives the hose its desired diameter and wall thickness.
This process requires a high level of precision. Maintaining consistent temperature control and pressure is vital to ensure uniformity in the hose’s thickness and durability. Any inconsistency during extrusion can result in weak spots or structural defects in the hose, which could compromise its performance under pressure or extreme conditions.
Step 3: Reinforcement for Strength
While basic PVC hoses are flexible and versatile, many industrial applications require hoses that can withstand extreme conditions, such as high pressure, chemical exposure, or abrasive materials. This is where reinforcement comes into play.
For added strength, PVC hoses are often reinforced with layers of polyester fiber, nylon braids, or steel wire. The reinforcement is typically embedded between two layers of PVC, creating a multi-layered hose structure. This reinforcement allows the hose to handle higher pressures, maintain its shape under stress, and resist kinks or collapse.
For example, steel wire reinforcement is commonly used in hoses designed for suction applications, such as in vacuum systems or material handling. Fiber-reinforced PVC hoses, on the other hand, are used in industries that require flexibility along with the ability to handle moderate pressure, such as in agriculture or air compressors.
Step 4: Cooling and Curing
Once the PVC hose is extruded and reinforced, it undergoes a cooling process. Cooling is a crucial step, as it solidifies the hose’s structure, allowing it to retain its shape and properties. Typically, the hose is passed through a water bath or air-cooled, depending on the hose type and the desired characteristics.
In some cases, additional curing processes are applied, especially for specialized hoses designed to handle extreme conditions. These curing steps may involve subjecting the hose to controlled heat treatments, which further enhance its strength, flexibility, and resistance to various environmental factors.
Step 5: Quality Control and Testing
Quality control is an essential aspect of PVC hose manufacturing. Manufacturers implement rigorous testing protocols to ensure that each hose meets the required industry standards for durability, flexibility, pressure tolerance, and chemical resistance. Common tests include burst pressure testing, elongation tests, and checks for leaks or cracks under pressure.
Visual inspections are also performed to identify any surface defects, such as air bubbles, uneven thickness, or cuts. These tests are critical in ensuring that only high-quality, reliable hoses make it to market, offering users the confidence that the product will perform as expected in demanding industrial environments.
Step 6: Customization and Specialized Applications
Not all PVC hoses are created equal, and manufacturers understand that different industries have unique needs. Customization is a key part of PVC hose production. Depending on the application, manufacturers can tailor the hose’s size, material composition, color, and even specific properties like UV resistance or anti-static qualities.
For instance, in the food and beverage industry, PVC hoses need to be food-grade, meaning they are non-toxic, odorless, and free from harmful chemicals. In chemical processing, hoses often need to be reinforced to resist the corrosive effects of acids or solvents. Customization ensures that each industry receives a product tailored to its specific operational requirements.
Step 7: Packaging and Distribution
After the hoses pass all quality checks, they are cut to length, coiled, and packaged for distribution. Some PVC hoses are packaged in reels for easy transport and installation, while others are sold in pre-cut lengths depending on customer specifications. Proper packaging ensures that the hoses are protected during transport and storage, maintaining their integrity until they reach the end user.
Conclusion: From Raw Material to Essential Industrial Solution
The journey of a PVC hose, from raw material to reinforced strength, is a sophisticated process that combines science, engineering, and craftsmanship. Each step in the manufacturing process is designed to enhance the hose’s durability, flexibility, and performance. Whether it’s handling high-pressure fluids in an industrial setting or providing flexibility in a home garden, PVC hoses are built to last, ensuring industries around the world have the reliable solutions they need to operate efficiently.
By understanding the complexities behind PVC HOSE Manufacturer production, we can appreciate the advanced engineering that goes into making these versatile and robust products, ensuring they remain at the forefront of industrial innovation.