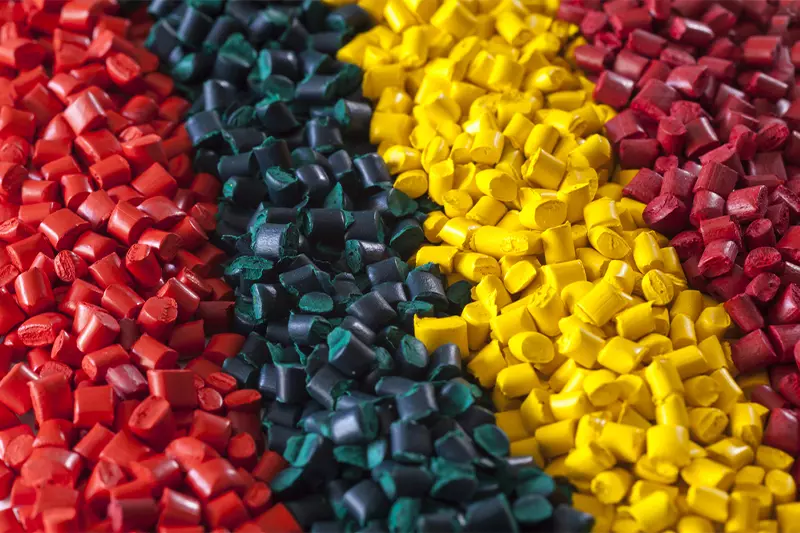
Plastic production is an industry marked by innovation and adaptability, and one essential element that plays a vital role in the manufacturing process is Masterbatch. This article explores what Masterbatch is, its types, and its significance in plastic production. Understanding how Masterbatch enhances plastic materials can provide a deeper insight into why it’s crucial for manufacturers.
What is Masterbatch?
Masterbatch is a solid additive, usually in a granular form, that is incorporated into plastics to add specific properties or colors. It is made by blending pigments, additives, and carrier resins. During plastic production, Masterbatch is introduced to raw polymers, allowing manufacturers to customize the final properties of the plastic, such as color, strength, and UV resistance. By using Masterbatch, manufacturers can achieve a consistent and uniform distribution of color or other desired features across the plastic material.
Types of Masterbatch
Masterbatch comes in various types, each designed to add a unique property to the plastic. Here are some commonly used types:
1. Color Masterbatch
This is the most widely used type, which provides the desired color to the plastic. Color Masterbatch is made by combining pigments with a carrier resin that is compatible with the base plastic material. It ensures consistent color throughout the production process and enables customization of plastic products in virtually any shade.
2. Additive Masterbatch
Additive Masterbatch enhances the performance of plastics by introducing specific additives. This category includes several subtypes based on the function:
- UV Stabilizers: Protect plastic from damage caused by sunlight exposure.
- Antioxidants: Prevent the degradation of plastic due to oxidation.
- Anti-static Agents: Reduce static electricity build-up on plastic surfaces.
3. Filler Masterbatch
Filler Masterbatch is used to reduce the amount of polymer needed in plastic production, making the process more economical. Common fillers include calcium carbonate and talc, which not only reduce costs but also improve properties like rigidity and opacity in certain plastics.
4. Flame Retardant Masterbatch
Certain applications, especially in the construction and electronics industries, require plastics that are resistant to fire. Flame Retardant Masterbatch provides these properties by introducing flame-resistant compounds into the plastic, reducing its flammability.
Benefits of Using Masterbatch in Plastic Production
Using Masterbatch in plastic production offers numerous benefits, from enhancing the quality of the final product to making the production process more efficient. Here’s how:
1. Consistent Quality and Appearance
One of the primary advantages of using Masterbatch is the ability to achieve a uniform color and appearance in plastic products. This consistency is especially important for items that need to meet strict aesthetic standards, like consumer goods and automotive parts.
2. Cost Efficiency
Masterbatch reduces production costs by allowing manufacturers to introduce color and additives without overusing expensive raw materials. It also minimizes waste, as the plastic is less likely to be discarded due to uneven color or property inconsistencies.
3. Enhanced Physical Properties
Different Masterbatches improve the durability, strength, and other physical properties of plastic. For instance, adding UV stabilizers can increase the lifespan of plastics exposed to sunlight, while antioxidants prevent degradation caused by exposure to oxygen and heat.
4. Environmentally Friendly Options
Masterbatch production has become more eco-friendly, with some manufacturers producing biodegradable or recyclable Masterbatch options. Using these helps reduce the environmental impact of plastic production and can contribute to more sustainable manufacturing practices.
Masterbatch Production and How it’s Used in Manufacturing
The process of producing Masterbatch involves melting the base polymer, then adding pigments and additives to create a concentrated, homogenous mix. This mixture is cooled, cut into granules, and then used in plastic manufacturing. Here’s a look at how it fits into the overall production process:
1. Injection Molding
In injection molding, Masterbatch is blended with raw polymers to produce items like bottle caps, containers, and automotive parts. The precise color and property control that Masterbatch offers make it ideal for products requiring high standards.
2. Extrusion
Extrusion is a process in which Masterbatch is mixed with polymers to form continuous shapes, such as pipes and sheets. Using Masterbatch in extrusion enables even color and property distribution throughout the product’s length.
3. Blow Molding
Blow molding involves inflating heated plastic into molds to create hollow items like bottles. Here, Color Masterbatch is especially useful to achieve vibrant, consistent colors in consumer packaging.
Future Trends in Masterbatch
As the plastic industry evolves, so does the Masterbatch market. Innovations are being made to meet environmental regulations and demand for high-performance plastics. Here are some trends to watch:
1. Biodegradable Masterbatch
With the shift towards sustainability, biodegradable Masterbatch options are gaining popularity. These are designed to degrade under specific environmental conditions, making them ideal for single-use plastics and eco-friendly products.
2. Smart Masterbatch
New developments in “smart” Masterbatch involve materials that can change color or transparency in response to environmental changes, such as temperature or light. These advancements could transform industries like packaging, where intelligent materials are increasingly sought after.
3. Customization and Digitalization
The rise of digital technologies in manufacturing is making it easier to customize Masterbatch solutions for specific customer needs. Through advanced color-matching and rapid formulation technologies, manufacturers can develop tailored solutions faster and more efficiently.
Conclusion
Masterbatch plays a pivotal role in the plastic production industry by providing a cost-effective and efficient way to add color and properties to plastics. From enhancing aesthetic appeal with Color Masterbatch to improving performance through Additive Masterbatch, its applications are vast and continually evolving. As the industry moves toward sustainability and innovation, Masterbatch will remain an essential component in meeting the demands of modern plastic production.
Whether for automotive, consumer goods, or packaging, the use of Masterbatch allows for flexibility, quality, and the ability to innovate, ensuring that plastics continue to meet diverse industry needs while reducing environmental impacts.